Infrared thermography is a technology that is being utilized more widely by building inspectors. But what is infrared thermography? How can it be used to help inspect a home or commercial structure? What are its limitations? George Green, level one thermographer and home inspector with Boggs Inspection Services, is here to tell you all there is to know about this technological tool that uses heat differences to create a visual picture of the spaces inside and outside buildings.
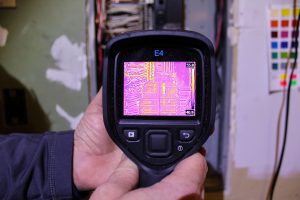
What is Infrared Thermography?
Infrared thermography is a tool that captures wavelengths just a little longer than those on the visual spectrum, which are invisible to the human eye. The technology can be used in the form of a camera to create visual representations of surface heat. Surfaces give off different levels of radiation and infrared thermography displays those distinctions. Then, a trained technician uses that picture to assess conditions in the structure, from insulation variations, heating and cooling efficiency, water leaks, electrical issues and more. “There are so many applications these cameras can be used for in an inspection,” says George.
Making Invisible Problems Visible
Variations in temperature are not always perceptible. By the time electrical issues become visible to the human eye, the damage may already be extensive. Infrared thermography can be used to uncover overheating in electrical panels and to look at wires and breakers for a more thorough picture of components that may be faulty.
Infrared thermography also has a place in commercial structure inspections. It is especially handy for use in flat roofs, where it can detect minor leaks and roof membrane issues before they become extensive, and expensive, problems.
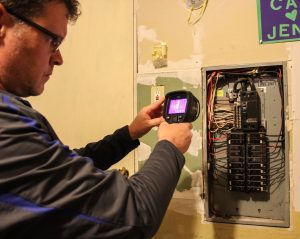
Infrared thermography can be used to inspect insulation, either in new buildings to ensure work was done properly, or in older buildings where there can be concerns about insulation settling. Temperature variations between wall sections or differences from the ceiling down to the floor are all clues a trained eye can use to assess a problem.
Showing the Scope of a Problem
Infrared technology can be used along with other tools to measure the scope of a problem. For instance, infrared can detect the spread of moisture below a surface. “You can’t always touch and see how much moisture is there, or how widespread the leak is,” says George. When a wax ring begins leaking around the toilet, the damage can occur to the subflooring before any visual damage like buckling is evident. “The cameras can detect minute temperature differences to give a visual representation of where the moisture has spread, whether it is just localized around the toilet, or if it has spread through the subfloor and even up the wall,” he explains.
Stains can be a sign of leaks, but infrared can help an inspector tell if the stain is the result of an active leak, or just the remnant of a problem that has been remedied, and just needs simple surface repair.
Limitations
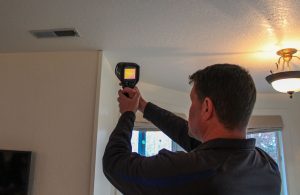
Utilizing infrared technology can help uncover a wide range of information about the home, but the technology is limited by the training and experience of the user. For instance, thermography can be utilized in home efficiency and energy audits, looking for places where the home is leaking heat in the winter or cool air in the summer. If the test is not set up properly, homeowners could find themselves with erroneous results, which could fool them into thinking their home is more energy efficient than it is, or lead them to believe there are problems that need to be fixed where no actual problem exists. “It’s a great tool when you know how to set it up properly to take good readings,” says George. “You can get a lot of good information to relay to the customer.”
Besides properly setting up to use thermography, interpretation of the infrared data is crucial. The skills and experience to understand what different temperature readings mean are important when it comes to differentiating between an electrical overheating concern and a water leak.
All the inspectors on the Boggs team are trained in the use of infrared thermography, and George is working with them to create in-depth reports for customers that are looking for specific assessments, such as electrical panel inspections or flat roofs. If you’d like a residential or commercial inspection that uses the latest technology, like infrared thermography, to get a thorough picture of your structure, give Boggs Inspection Services a call at 360-480-9602 or visit them online at the Boggs Inspection Services webpage.
Sponsored