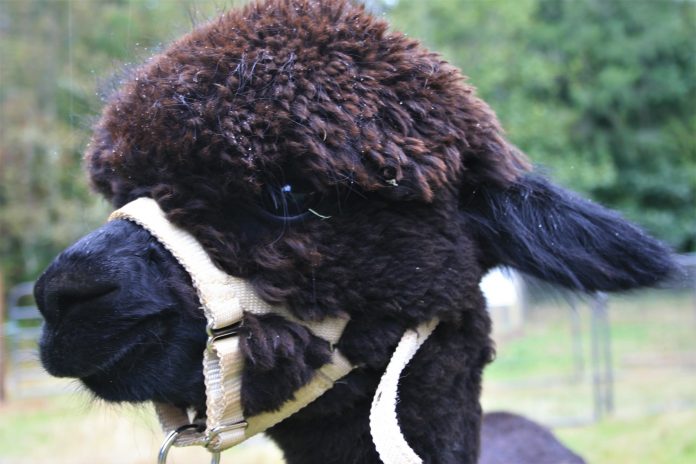
Hand crafted sweaters, socks and rugs are coming from Thurston County alpacas, their owners and talented artisans. Alpaca farms in Olympia and Yelm are active in the cycle of raising alpacas and milling the wool. These farmers and crafters are passionate about what they are creating, which involves a lengthy process from animal to finished fiber product.
After the yearly shearing process, the wool is cleaned by hand, or skirted, for large debris and stains. Next, it’s loaded into a large washing machine with divided sections, a bit like a home washer, agitating, draining and spinning. Each step in the process is key to ensuring a quality product.
“Although every step of the process from shearing to finished product is important,” says Jean Van Effen of Tahoma Vista Fiber Mill and La Vida Alpacas, “getting the fiber clean without damaging it is the most important step. If something goes wrong in one stage, it affects everything down the road.”
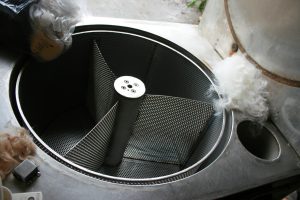
After the wool is cleaned, it is laid out to dry on racks. When dry, the now smaller clumps of hair are put into what Jean’s husband, David Bagshaw, calls the cloud machine, which grabs and fluffs the clumps, further separating the individual fibers. Fibers land inside a cupboard in a deep, pillowy cloud, the individual strands now becoming more visible.
Next, rolling barrels in the carding machine further separate the fluffed fibers, pulling them into alignment with one another. The combs are tiny metal spikes curved backward much like those on a cat’s tongue. The product of the carding machine is batt, a wide, thinly layered blanket like piece. Batt can go on to two different destinations from this point, to the roving deck, which narrows the wide batt into a long, quite transparent, fluffy rope, or it may go on to a hand spinning process.
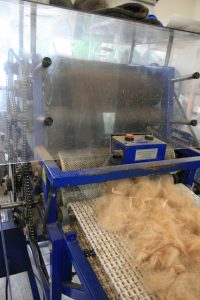
To become a rug though, batt exits the carding machine to a rug yarn maker, which forms the batt into a thick, rope product that can be used for rugs, chair seats, coasters and trivets. When the batt leaves the carding machine as a wide blanket, it crosses over a string. The string turns and twists, crossing sideways, the batt being pulled over as it goes, forming a thicker string, a rope of wool called core spun yarn, the core of which is the string.
Core spun yarn destined for rugs, goes through another series of stages. The rope of yarn is laid in the shape of the desired product. For example, if an oval rug is the goal, the core spun yarn is laid in the shape of an oval, starting at the center and circling outward, on the flat surface of an agitation machine called a “wet filter.” Exposure to heat and soap, causes the scales on the fiber follicles to expand and grab onto those of others near them. Fibers dry and bind even closer together, (think of your infamous wool sweater that shrinks in the wash!) However, when the desire is a rug that should keep its shape, heat, soap, agitation and the shape-keeping control of a flat press help create that strength. The rug is then laid over felting, and a warm, flat wash promotes more fiber binding. The process continues in repetition until the desired connection and shape is achieved.
Each Fiber Counts
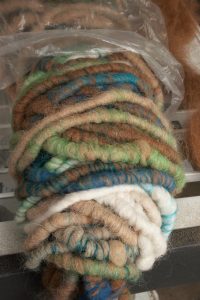
An alpaca hair fiber is thinner than a human hair and is also hollow, making it a warm insulator. An animal with the optimum hair fiber is the goal of breeders. Alpaca hair fibers are under scientific scrutiny for careful planning so the ultimate results can be achieved through breeding.
“When making breeding decisions for optimum results, we look closely at the conformation and fleece characteristics of both the dam and sire,” says John and Susan Dana of 3D’s Alpacas in Olympia. “If we can produce a cria that has improved upon the traits of both parents, we are delighted that we have done our job properly.”
Raising alpacas goes beyond the science and breeding through. The alpacas and breeders have somewhat of a symbiotic relationship that is special. “One of the most satisfying things about raising Alpacas is that it gives us a purpose to get our lazy butts out of bed to care for these wonderful little creatures each and every day!” say the Danas who specialize in Huacaya alpacas. “It has also connected us with some other awesome alpaca enthusiasts through our local Alpaca Association of Western Washington. It has been the perfect transition into our retirement.”
Alpaca wool holds great meaning for Jean and her husband David at the Tahoma Vista Fiber Mill as well. “Artisan mills are vital to the U.S. Alpaca industry,” they share. “Raising alpacas ourselves helps us to understand the processing needs of our fellow owners and helps us to provide education for them to maximize their profit from their fiber production. We are passionate about alpacas and natural fibers in general. They are eco-friendly and sustainable. Our mill provides employment to several people and provides local and regional fiber farmers with additional revenue streams from their production.”
Alpaca fibers, raised, shorn and milled in Thurston County, are used in clothing, rugs and a variety of household items. Farms such as 3D’s Alpacas in Olympia and the Tahoma Vista Fiber Mill in Yelm area available for tours.